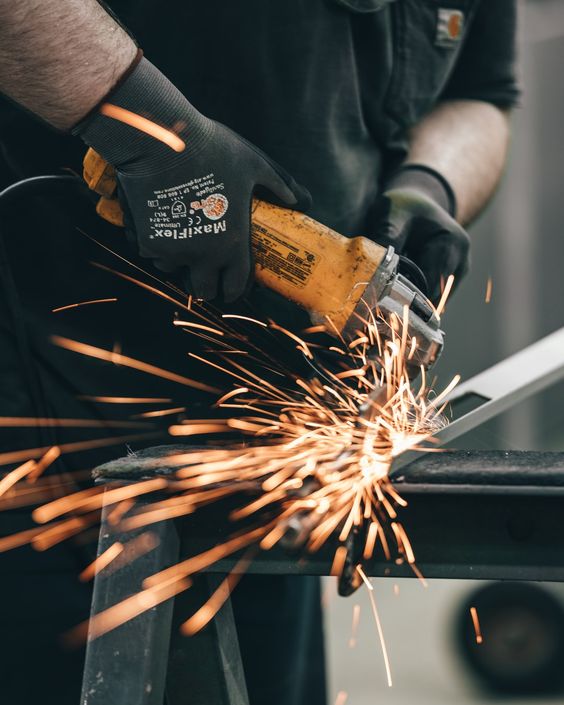
Metal are a big part of our day to day life. Common metals like Mild Steel, Stainless Steel, Aluminum, Copper, Zinc, Nickel, Tin, Lead and precious metals like Gold, Silver, and platinum each have unique properties, purposes — and weaknesses. Metal finishing addresses these potential weaknesses and helps increase the strength and capabilities of the metal products. In the realm of manufacturing and engineering, metal finishing stands as a crucial step in transforming raw metal surfaces into refined, functional, and aesthetically pleasing products. Metal finishing encompasses a range of techniques that not only enhance the appearance of metal objects but also improve their durability, corrosion resistance, and performance. This blog post delves into the metal finishing process, shedding light on its various techniques, applications, and the significant impact it has on diverse industries.
Understanding Metal Finishing:
Metal finishing refers to the application of a series of processes and treatments to alter the surface of metal objects. These techniques aim to enhance the appearance, protect against corrosion, improve wear resistance, facilitate bonding, and enable electrical conductivity. Metal finishing processes can be broadly classified into mechanical, chemical, and electrochemical methods, each serving specific purposes. Processes include Cleaning, Polishing, Plating, Anodizing, Coating, Painting, etc., Each method serves a unique purpose, and the choice of technique depends on the desired outcome, the metal being treated, and the industry requirements.
Common Metal Finishing Techniques:
- Blasting: Blasting, also known as abrasive blasting, Sand Blasting, Shot Peening, is a process used to clean, etch, or prepare surfaces by propelling abrasive materials at high velocity. This is typically done using compressed air or mechanical force. The shot particles impact the surface, effectively removing contaminants, rust, paint, or unwanted coatings.
- Galvanizing: Galvanizing is a process used to apply a protective coating of zinc onto steel or iron surfaces. The aim of galvanizing is to provide corrosion resistance to the underlying metal, extending its lifespan and enhancing its durability. The material is then dipped into a bath or tank of molten zinc, ensuring complete coverage and allowing the zinc to bond metallurgically with the steel or iron surface.
- Plating: Electroplating and electroless plating involve depositing a layer of metal onto the surface of an object through an electrolytic or chemical reaction. This technique enhances the metal’s appearance, provides corrosion resistance, and offers additional benefits like improved conductivity.
- Anodizing: Anodizing is an electrochemical process used primarily on aluminum surfaces. It creates an oxide layer, increasing corrosion resistance and enabling the application of various colors and finishes.
- Passivation: Passivation involves treating stainless steel with an acid solution to remove surface contaminants and improve its corrosion resistance.
- Polishing and Buffing: Mechanical processes like polishing and buffing utilize abrasives to remove imperfections, smooth the surface, and enhance the object’s visual appeal.
- Powder Coating: Powder coating involves applying a dry powder to the metal surface, which is then cured through heat to form a durable, protective layer. This technique offers excellent corrosion resistance, durability, and a wide range of colors and finishes.
- Painting: Painting is a process of applying a liquid coating, known as paint, onto a surface to enhance its appearance, protect it from damage, or convey a specific message. The choice of paint type, color, and application technique depends on the desired outcome and the properties of the surface being painted.
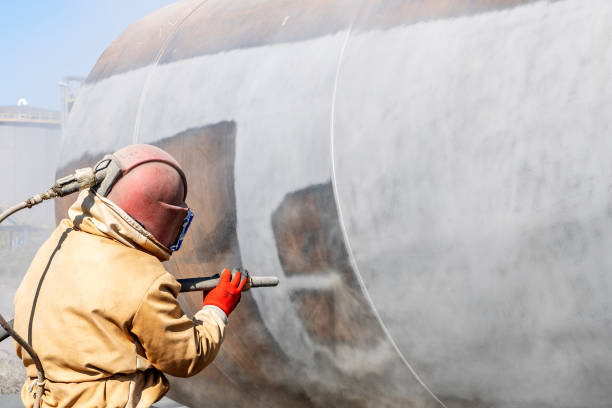
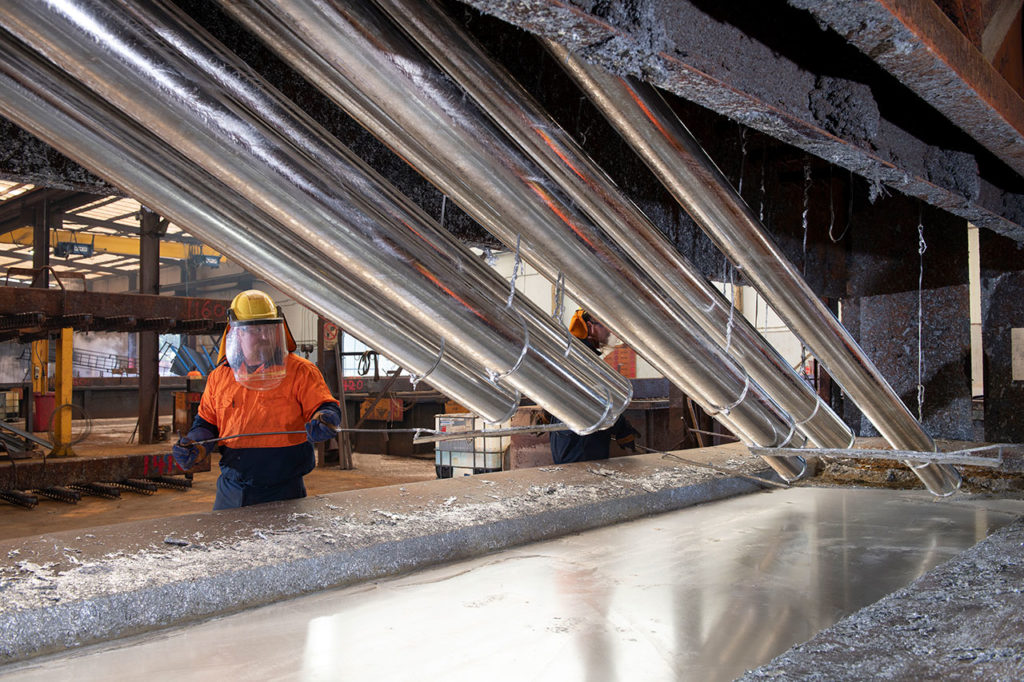
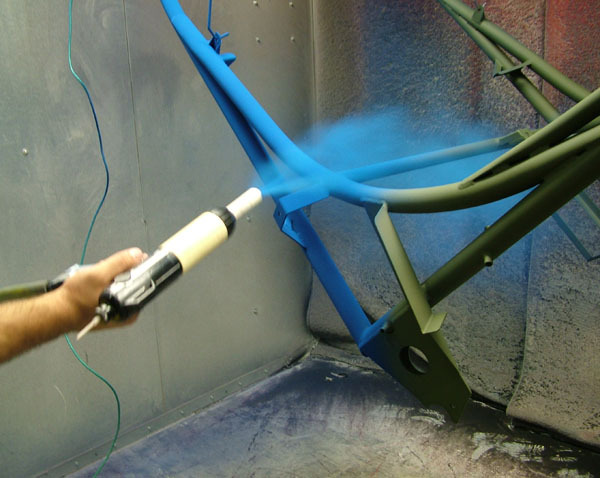

Benefits of Metal Finishing:
Enhancing Aesthetics:
One of the primary reasons for metal finishing is to enhance the visual appeal of metal products. Polishing and buffing techniques create a smooth, reflective surface, giving metals a lustrous and attractive appearance. Additionally, various coatings like paints, enamels, and powder coatings can be applied to add color, texture, and protection against wear and corrosion. Metal finishing transforms raw metal surfaces into visually appealing and marketable products.
Improving Corrosion Resistance:
Corrosion is a significant concern for metal components, leading to deterioration, reduced lifespan, and potential safety hazards. Metal finishing processes like electroplating, anodizing, and galvanizing form protective layers that shield metals from corrosive elements. These coatings act as a barrier, preventing moisture and environmental factors from directly contacting the metal surface, thereby extending its lifespan and maintaining its performance.
Increasing Durability and Wear Resistance:
In industries where metals are subject to heavy use or abrasive conditions, metal finishing can significantly enhance durability and wear resistance. Hardening treatments, such as heat treatment and nitriding, increase the surface hardness of metals, making them more resistant to scratches, abrasion, and impact. Additionally, the application of protective coatings like ceramic or polymer-based materials further improves wear resistance, ensuring the longevity of metal components.
Enhancing Conductivity and Solderability:
In electronic and electrical industries, metal finishing techniques are used to improve the conductivity and solderability of metal surfaces. Electroplating with materials like gold or silver can enhance electrical conductivity, ensuring efficient transfer of current. Surface treatments like solder plating increase the solderability of metals, allowing for reliable solder joints in circuit boards and electronic assemblies.
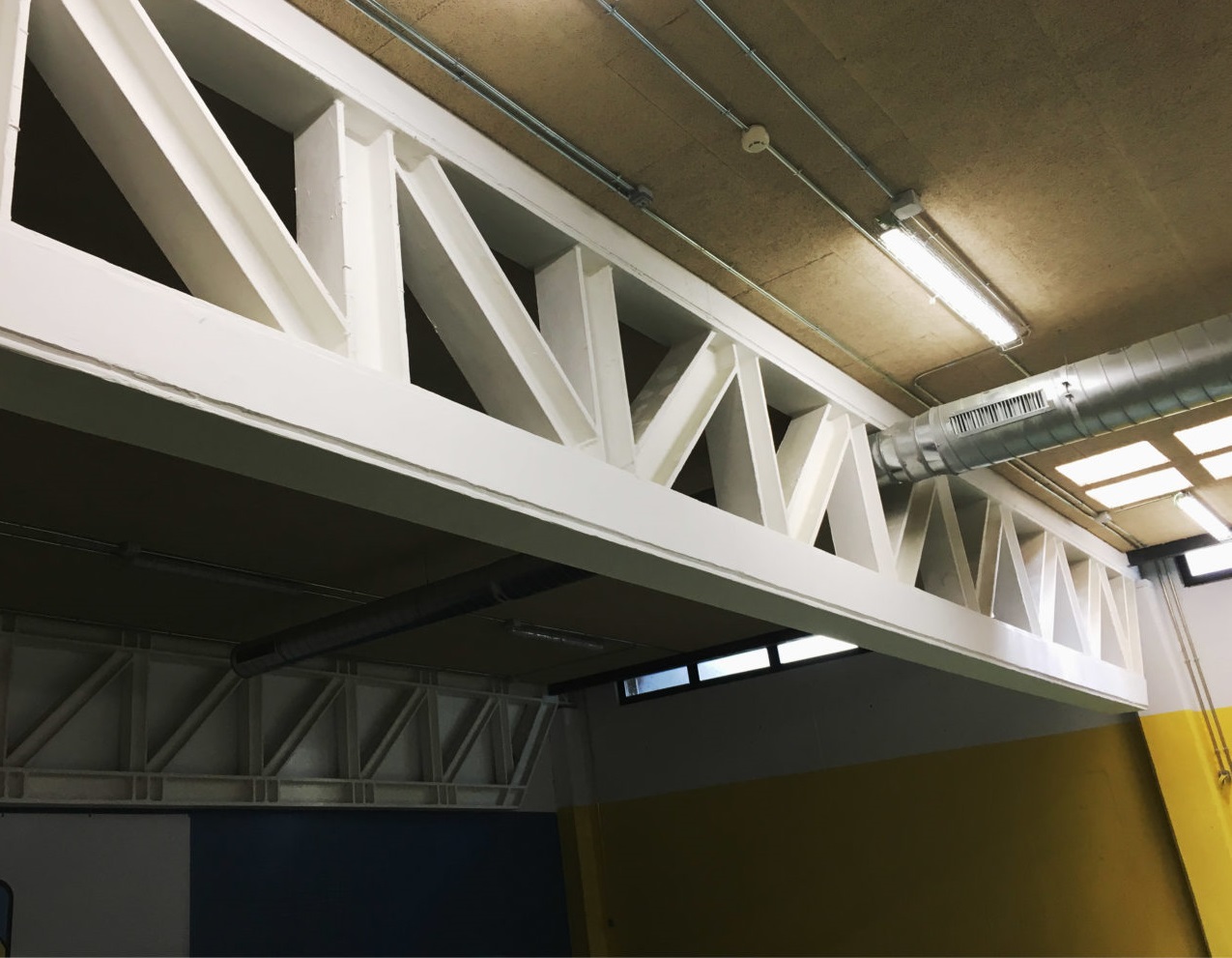
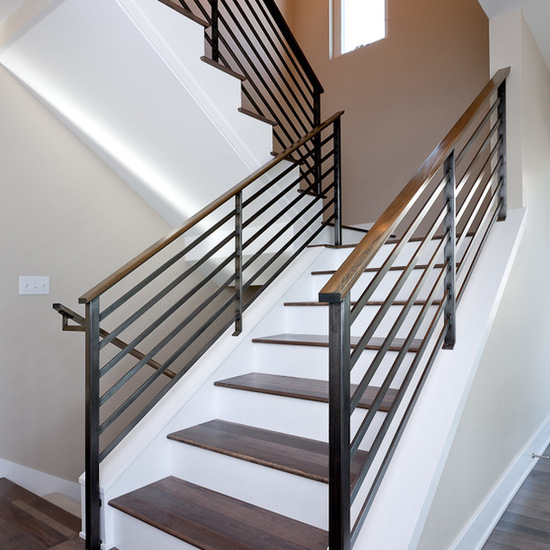
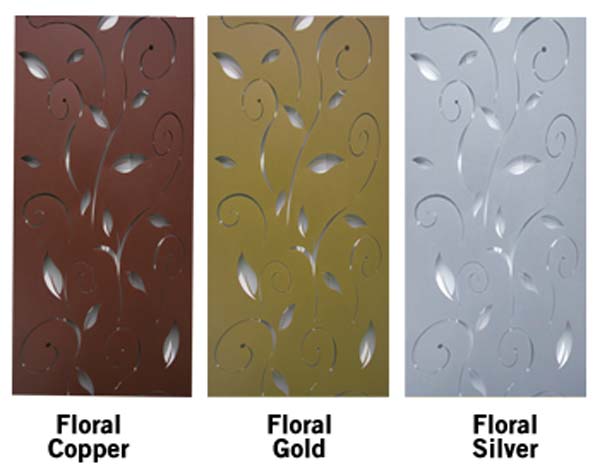
Conclusion:
Metal finishing is a vital process in the world of Manufacturing and Engineering, offering numerous benefits to industries ranging from automotive and aerospace to architecture and consumer goods. The diverse range of techniques available allows manufacturers to tailor finishes to specific requirements, simultaneously improving the aesthetics, functionality, durability, and environmental impact of metal objects. As technology continues to advance, we can expect further innovations in metal finishing, paving the way for even more remarkable products in the future.